On Saturday, October 18, hundreds of undergraduate students shared the results of their projects during SURF Seminar Day. The event provides students with the opportunity to discuss and explain their research to individuals with a wide-range of expertise and interests.
For someone like Edward Fouad, a junior at Caltech who has always been interested in robotics and mechanical engineering, it was an ideal project: help develop robotic technology that could one day fly on a NASA mission to visit and sample an asteroid.
Fouad spent 10 weeks this summer as part of the Summer Undergraduate Research Fellowship (SURF) program working in the lab of Aaron Parness, a group leader at JPL, where researchers are designing, prototyping, and refining technology for a device called a microspine gripper. Looking something like a robotic circular foot with many toes extending radially outward, such a gripper has the ability to grab onto a rocky surface and cling to it even when hanging upside down.
That makes it a good candidate to be included in the robotic capture phase of NASA's Asteroid Redirect Mission, which aims to capture an asteroid and haul it into lunar orbit where robotic and manned missions could study it more easily. One of two concepts that NASA is currently considering for that mission involves using robotic arms to grab a boulder for return from a much larger asteroid. Microspine gripper technology is being evaluated for use on these robotic arms.
Researchers at JPL have been working on this technology for almost five years. The latest version of the gripper is made entirely of metal and consists of two concentric rings of carriages—the toe-like appendages that stick out from the gripper. Each of those carriages is in turn made up of a number of "microspines" with steel hooks at their tips. When the gripper makes contact with a rocky surface, the carriages extend downward onto the rock and then pull inward toward the gripper's center. Because the carriages and microspines all move independently, the gripper is able to conform well to the rock's nooks and crannies.
For his SURF project, Fouad helped with the construction of the latest gripper prototype and worked on improving the design of the microspines for the next generation. In particular, his goal was to design a metal microspine that could conform to a rocky surface and stretch as needed toward the center of the gripper. One of the key elements in such a design is a compliant flexure, a material that can bend and flex, allowing each hook to move independently of its neighbors, to grab onto the crags of an uneven surface. In the past, elastic polymers and metal extension springs have been used for this purpose, but elastic polymers cannot stand up to the extreme temperatures of space, and the springs greatly increase the complexity of the gripper's design and complicate the manufacturing and assembly processes. A different metal option was needed.
"I started by brainstorming many different flexure designs, modeling them on the computer with CAD software, and laser cutting them out of acrylic to test their compliant properties," Fouad says. After repeating that process and improving the designs over several weeks, Fouad and Parness settled on two designs to prototype in metal and test on different rock types. In the end, one of Fouad's designs worked so well in bench-top tests that Parness's group is now incorporating it into their new gripper design.
"Edward did a great job this summer," says Parness. "The SURF program provides a great balance; it ensures an educational experience for the student but also provides a lot of value to the projects and mentors. I always try to work with the students before the summer so that the SURF projects provide some autonomy but give the students a chance to work toward something that could make a long-term contribution to the main project. Edward's project was a good example."
Fouad says he went into the SURF project with a lot of relevant experience. A statics and material mechanics course (ME 35—now ME 12) had provided him with the background he needed to understand how the microspine toes of a particular geometry would deform under different loading conditions. A mechanical design and fabrication class (ME 14) taught him important design skills. And, he says, "The experience I have gained leading the mechanical subgroup of the Caltech Robotics Team was invaluable for my work this summer. Through designing and constructing an autonomous underwater vehicle over the past year, I have acquired a great deal of design and machining techniques as well as the skills necessary to collaborate with others on a large group project."
Fouad says he loved working in Parness's lab and enjoyed having the freedom to pursue the design paths that he found most interesting and promising. And he says that he will now strongly consider pursuing a future career at JPL. "It is an incredible environment for someone looking for exciting robotics opportunities."
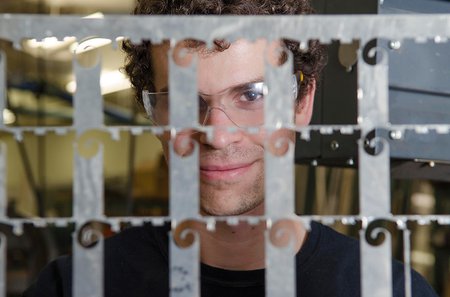
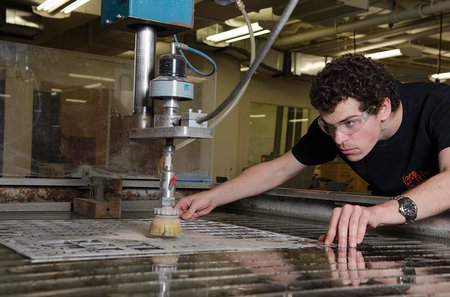
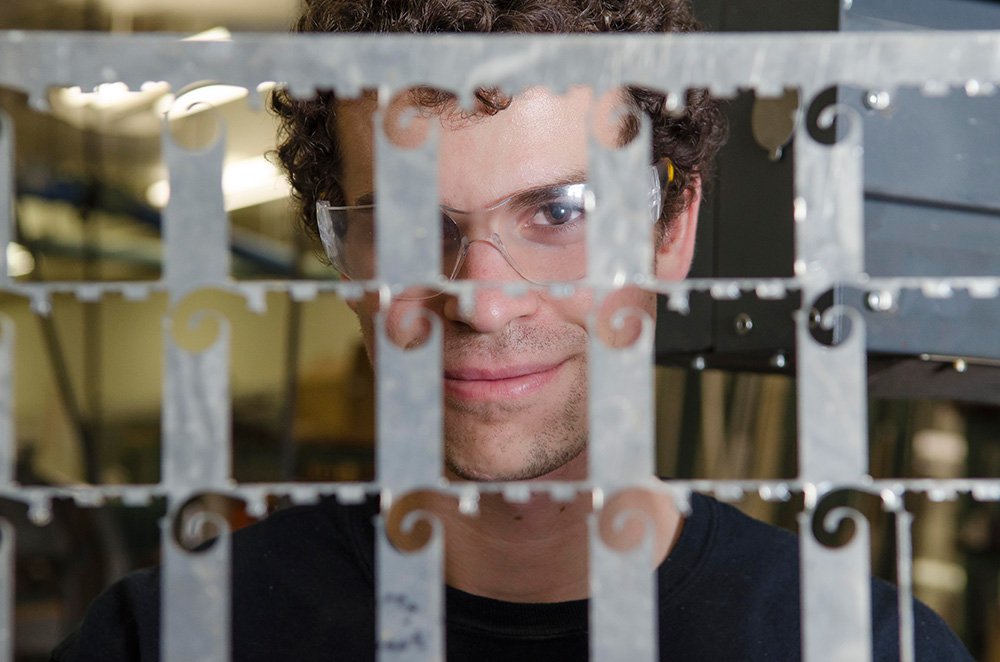
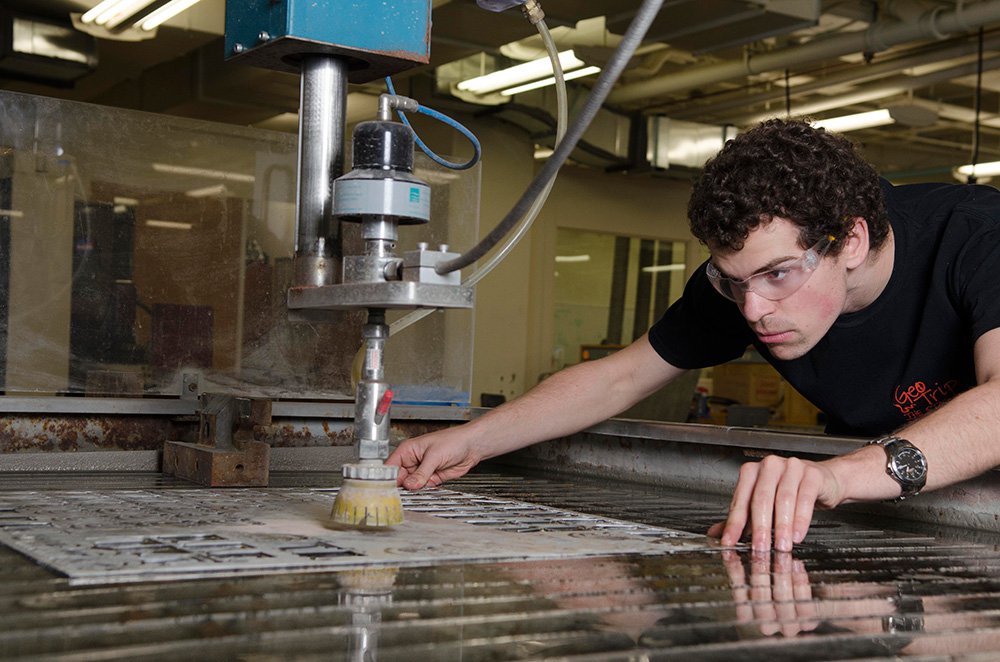